Vibroacoustic
Materials (VAMM)
Development of Metamaterials
In 1968, the Russian physicist Victor Veselago described a material with a negative refractive index, and in 1999, David R. Smith experimentally confirmed this. The term “metamaterial” was coined to describe material properties that do not occur naturally. Over the last 20 years, metamaterials have evolved in various physical domains. Metamaterials, such as the Vibroacoustic Metamaterials (VAMM) studied here, influence the propagation of waves. Market studies predict enormous growth potential for metamaterials. Vibroacoustic Metamaterials (VAMM) are a subset of acoustic metamaterials and influence the propagation of structure-borne sound as well as the radiation of structures through negative interference, negative effective stiffness, or mass, within a given frequency range.
Vibroacoustic Materials
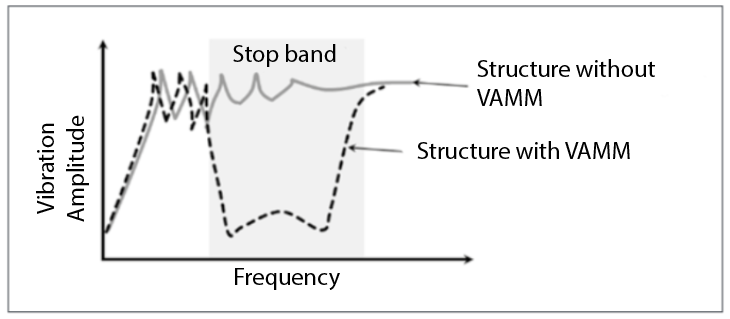
Schematic representation of a stopband in the frequency domain
Vibroacoustic Metamaterials (VAMM) are utilized to control vibrations in structures by suppressing specific frequencies. The metamaterial functions as a stopband filter, significantly reducing the propagation of mechanical vibrations and oscillations within the stopband frequency range. The realization of VAMM can be based on either the Bragg effect or local resonances. The Bragg effect leverages wave interference at a crystal lattice, while local resonators generate a virtual negative mass. VAMM can be fabricated from various materials, including recycled or biodegradable materials for sustainable applications. Active metamaterials offer weight, size, and flexibility advantages as resonance tuning is done electronically. These properties make them particularly attractive for lightweight construction and the creation of compact low-frequency absorbers, for example, in ventilation systems. Metamaterials open up possibilities for various and evolving application domains.
Design and optimization
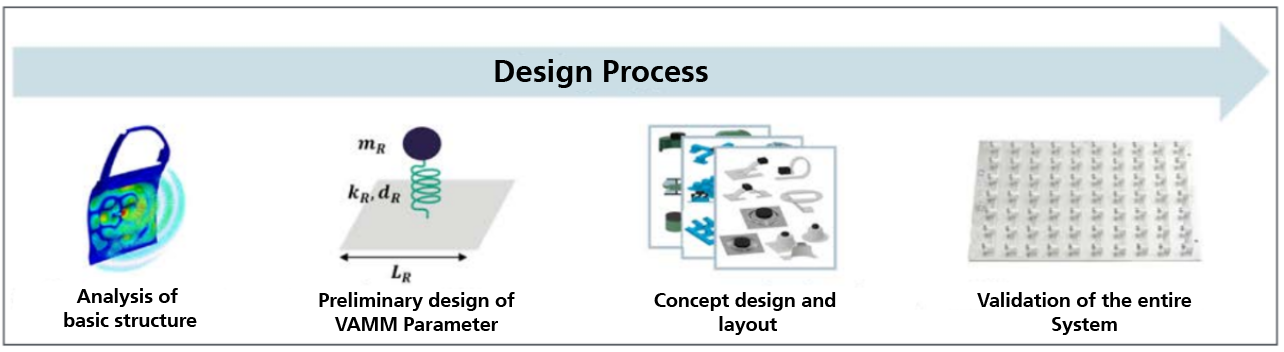
Design and optimizationDesign process for the holistic design of structural dynamic VAMM
A structured process for designing components with vibroacoustically modulated metamaterials (VAMM) has been developed. It begins with analyzing the basic structure and identifying excitation mechanisms. The adjustment of VAMM parameters considers wavelength and stopband characteristics. Design is based on the dispersion curve of the unit cell, where stopbands are identified as regions with no or strongly attenuated wave propagation. The necessary parameters are determined through a discrete mass-spring-damper system for the resonator. Subsequently, a concept is developed, and a parameterized finite element model is created. This allows for determining the relationship between geometric parameters and resonator properties. Selection of a specific parameter set can be manual or automatic, enabling automation of the design process. After optimization at the unit cell level, overall behavior is assessed, including the number and positioning of resonators. Proper Model Order Reduction (PMOR) methods are employed for efficient design, reducing model size and enabling efficient model evaluation, for instance, for optimization and uncertainty investigations.
Mass production
Various methods from the fields of plastic and metal processing are available for manufacturing VAMM. 3D printing is suitable for prototypes and individual parts, while thermoforming of thermoplastics or injection molding is used for mass production. Metal processing can be done through investment casting for precision small parts and die casting for large-scale production. Sheet metal parts can be cut using punching, waterjet, or laser cutting and shaped through bending, deep drawing, or roll forming. Manufacturing often involves joining elements, for which adhesive bonding serves as a reliable method. The selection of adhesive is crucial to avoid excessive damping of the vibration of the mass-spring-damper system. Manufacturing planning should be conducted in parallel with VAMM design to consider constraints early on. Environmentally friendly VAMM concepts, which do not require additives and consist of the same material as the base structure, are preferred due to manufacturing costs and recycling considerations.
The use of vibroacoustic metamaterials in a vehicle door
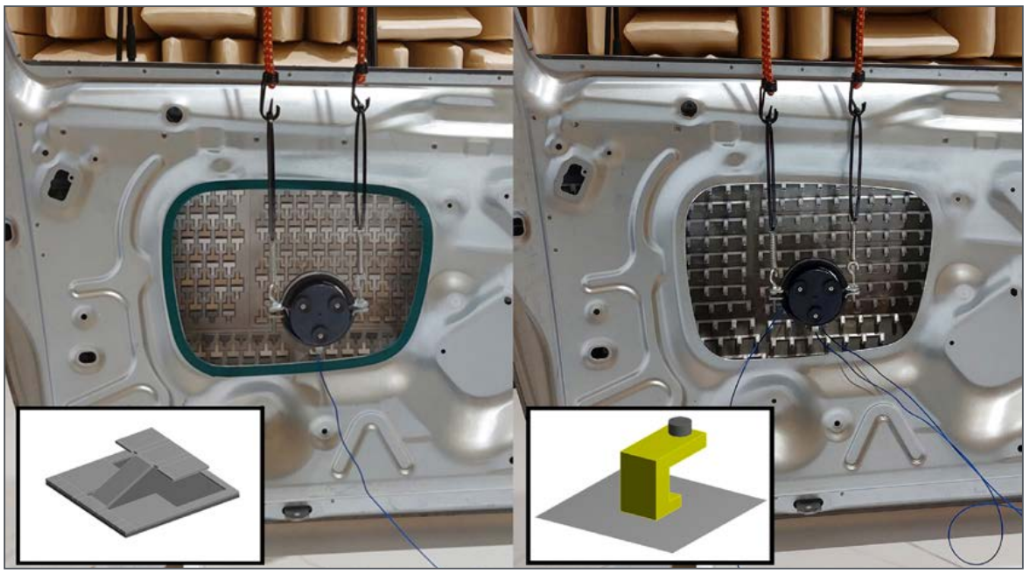
Vehicle door demonstrator with VAMM; left: metal concept, right: plastic concept
Vibroacoustic Metamaterials (VAMM) demonstrate promising potential for sound and vibration reduction in automotive engineering, exemplified by a vehicle door. Various resonator concepts were integrated into the door and tested for their acoustic properties. Metal and plastic bending beam resonators exhibited a level reduction of up to 30 dB compared to reference doors, particularly in the stopband regions. The VAMM variants exhibited broadband damping effects.
Acoustic metamaterials for a muffler.
The potential of acoustic metamaterials as mufflers in channels is demonstrated by arranging unit cells with resonators. Periodic composites and especially aperiodic arrangements enable stopbands for effective sound reduction. A tunable λ/4 resonator prototype in tube form was successfully realized using a 3D printer and shows variable resonance frequencies in the range of 200 to 600 Hz. A compact muffler concept with modular ring resonators offers flexibility and adaptability to different acoustic requirements. Another concept, the “spiral resonator,” shows promising attenuation values of over 20 dB in the frequency range of 300 Hz to 400 Hz.
Active metamaterials
An active metamaterial can actively influence a sound field by introducing a sound component or passively extract energy from the existing sound field by exciting the resonators. The resonator structures of active metamaterials are controllable through actuators. Active unit cells can be centrally or decentrally controlled. The design process is similar to that of passive metamaterials, with adjustments made to the unit cell impedance. An application in a ventilation duct demonstrates the formation of stopbands in the frequency range of 50Hz to 500Hz. A resonator cassette composed of active unit cells, coupled with Helmholtz resonators and electrodynamic speakers, exhibits higher insertion loss than conventional sound-absorbing panels.
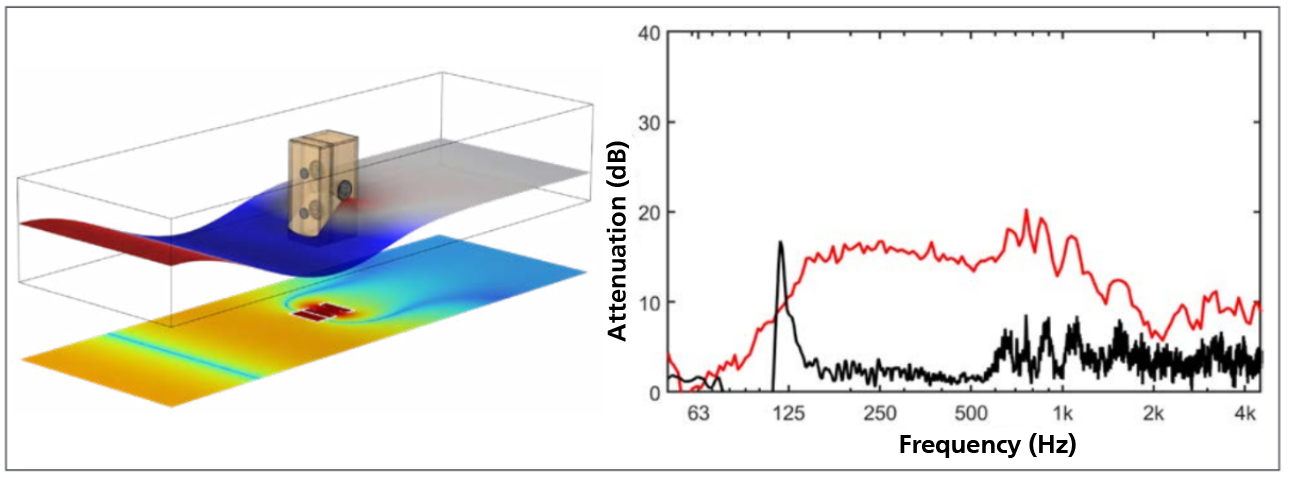