MetaVib Project
The goal of the project is
the implementation of the scientifically necessary work for the industrial utilization of vibroacoustic metamaterials (VAMM).
The implementation of the scientifically necessary work for the industrial utilization of vibroacoustic metamaterials (VAMM).
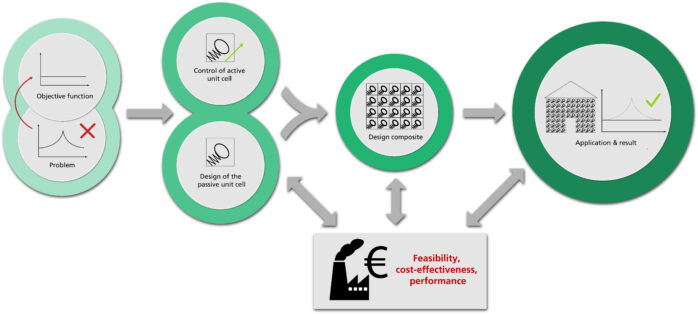
For the industrial utilization of VAMM, the following sub-goals are intended to be achieved:
- Development of a design tool for a comprehensive virtual design of VAMM in their application scenario.
- Testing of manufacturing processes for suitability for serial production (such as punching, forming, plastic 3D printing, hybrid casting).
- Development of a simplified and efficient signal processing for active VAMM.
Demonstrator "Vehicle Door"
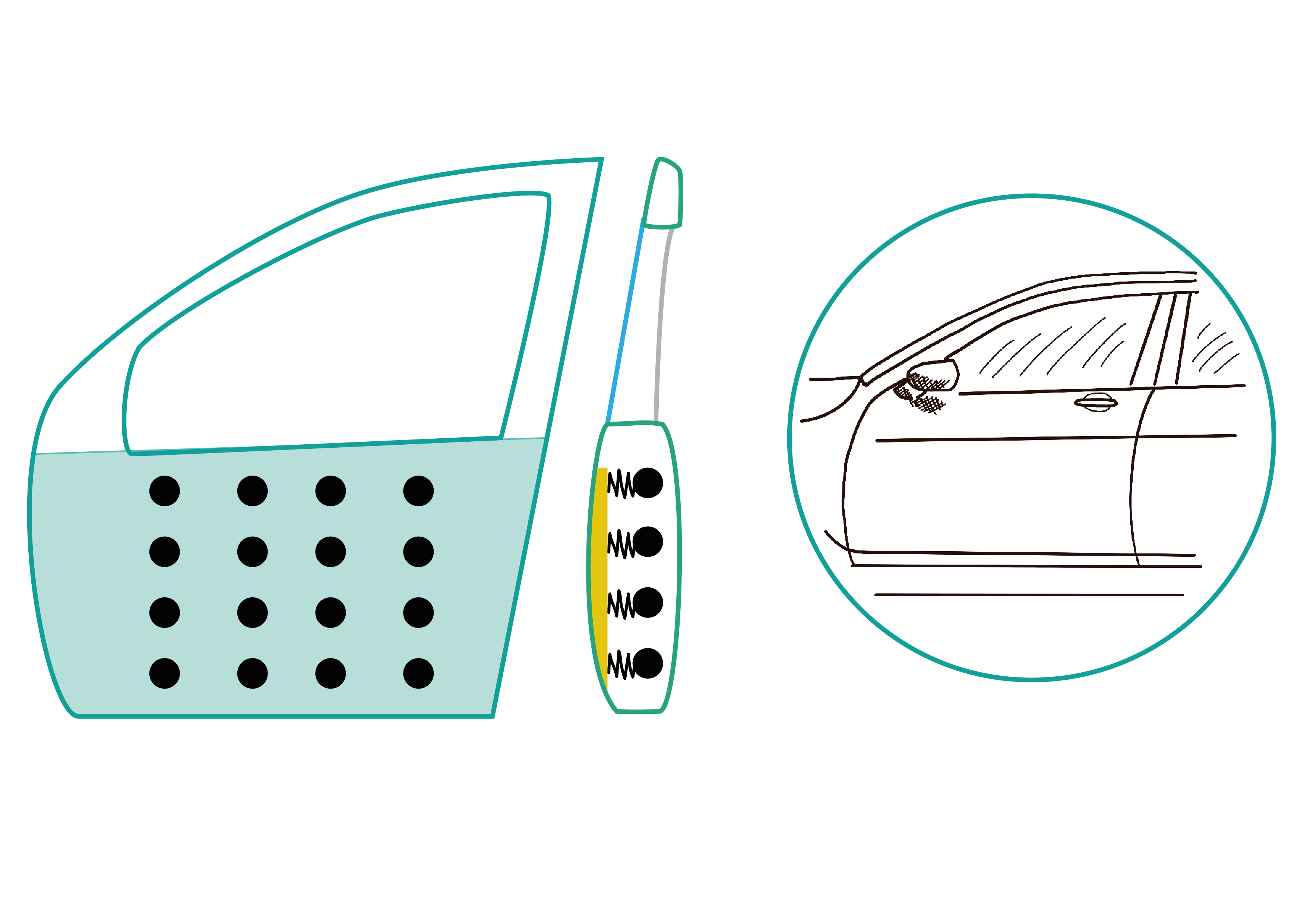
Schematic depiction of a vehicle door with integrated passive VAMM.
The vibroacoustic behavior of vehicle doors is relevant in terms of occupant comfort, which currently can be improved by increasing the area-specific masses. The use of VAMM for reducing road and wind noise as well as for reducing vibration excitation when closing the door offers the potential to achieve lightweight construction benefits and performance enhancements.
Demonstrator "Silencer"
To achieve sound attenuation at low frequencies, conventional silencer baffles require large layer thicknesses of porous absorber materials, which can compromise sound damping performance. By applying VAMM, it becomes possible to produce compact silencer baffles that are still effective at low frequencies.

Schematische Darstellung eines passiven Schalldämpferdemonstrators (grün) mit aktivierten Einheitzellen (orange)
Active VAMM
To achieve further enhancement of low-frequency effectiveness within a compact space, active sound control measures are necessary. The challenge in controlling the individual resonators of active VAMM is divided into linearization and stabilization areas. Conventional control concepts rely on the assumption of ideal, linear sensor and actuator behavior. Through intelligent transducer and system monitoring, coupled with adaptive signal processing strategies, the occurrence of unstable states in practical applications can be prevented. Since the unit cells interact with each other in composite form, an additional control approach is required to ensure ideal behavior in this scenario as well. Finally, the composite of idealized unit cells is made usable for the specific application through application-specific signal processing.
Manufacturing processes
In the project, manufacturing processes for industrial application of VAMM are being investigated. For metallic structures, new forming process chains are being developed for the high-precision manufacturing of intricate structures as well as for the integration of VAMM into sheet metal and body components. In the field of sheet metal forming, the aim is to further develop the stamping process for the production of VAMM sheet semi-finished products in such a way that the variation in resonator geometries is minimized to a defined minimum, and this can be reproducibly manufactured. In areas where these processes reach their limits, for example in terms of material or producible geometries, it is planned to cleverly combine them with typically slower processes, especially 3D printing processes (plastic and metal).